Książka opisująca życie i karierę obecnego dyrektora generalnego Apple, Tima Cooka, ukaże się już za kilka dni. Jej autor, Leander Kahney, udostępnił magazynowi fragmenty Kult Mac. W swojej pracy zajmował się między innymi poprzednikiem Cooka, Stevem Jobsem – dzisiejsza próbka opisuje, jak Jobs inspirował się w odległej Japonii, kiedy zakładał fabrykę Macintosha.
Inspiracja z Japonii
Steve Jobs zawsze był zafascynowany zautomatyzowanymi fabrykami. Po raz pierwszy zetknął się z tego typu przedsiębiorstwem podczas podróży do Japonii w 1983 roku. W tym czasie Apple właśnie wyprodukował swoją dyskietkę o nazwie Twiggy, a kiedy Jobs odwiedził fabrykę w San Jose, był niemile zaskoczony wysokim tempem produkcji błędy - ponad połowa wyprodukowanych dyskietek nie nadawała się do użytku.
Jobs może albo zwolnić większość pracowników, albo poszukać produkcji gdzie indziej. Alternatywą był dysk 3,5-calowy firmy Sony, wyprodukowany przez małego japońskiego dostawcę Alps Electronics. Posunięcie to okazało się słuszne i po czterdziestu latach Alps Electronics nadal stanowi część łańcucha dostaw Apple. Steve Jobs poznał Yasuyuki Hiroso, inżyniera w Alps Electronics, na targach komputerowych West Coast Computer Faire. Według Hirose’a Jobsa interesował przede wszystkim proces produkcyjny i podczas zwiedzania fabryki miał niezliczone pytania.
Oprócz japońskich fabryk Jobs inspirował się także w Ameryce, sam Henry Ford, który także spowodował rewolucję w przemyśle. Samochody Forda montowano w gigantycznych fabrykach, w których linie produkcyjne dzieliły proces produkcyjny na kilka powtarzalnych etapów. Efektem tej innowacji była między innymi możliwość złożenia samochodu w czasie krótszym niż godzina.
Doskonała automatyzacja
Kiedy Apple otworzyło swoją wysoce zautomatyzowaną fabrykę we Fremont w Kalifornii w styczniu 1984 roku, mogło złożyć kompletnego Macintosha w zaledwie 26 minut. Fabryka zlokalizowana przy Warm Springs Boulevard zajmowała powierzchnię ponad 120 stóp kwadratowych i miała wyprodukować do miliona komputerów Macintosh w ciągu jednego miesiąca. Jeśli firma miała wystarczającą ilość części, nowa maszyna opuszczała linię produkcyjną co dwadzieścia siedem sekund. George Irwin, jeden z inżynierów, którzy pomagali planować fabrykę, powiedział, że w miarę upływu czasu cel został skrócony nawet do ambitnych trzynastu sekund.
Każdy ówczesny komputer Macintosh składał się z ośmiu głównych komponentów, które można było łatwo i szybko złożyć. Maszyny produkcyjne mogły poruszać się po fabryce, gdzie były opuszczane z sufitu na specjalnych szynach. Pracownicy mieli dwadzieścia dwie sekundy – czasem mniej – na pomoc maszynom w dokończeniu pracy przed przejściem do następnej stacji. Wszystko zostało szczegółowo wyliczone. Apple udało się także zadbać o to, aby pracownicy nie musieli sięgać po niezbędne komponenty na odległość większą niż 33 centymetry. Komponenty do poszczególnych stanowisk pracy transportowano zautomatyzowanym samochodem ciężarowym.
Z kolei montażem płyt głównych komputerów zajmowały się specjalne zautomatyzowane maszyny, które mocowały do płyt obwody i moduły. Komputery Apple II i Apple III pełniły najczęściej funkcję terminali odpowiedzialnych za przetwarzanie niezbędnych danych.
Spór o kolor
Początkowo Steve Jobs nalegał, aby maszyny w fabrykach były pomalowane na odcienie, z których szczyciło się wówczas logo firmy. Nie było to jednak wykonalne, więc kierownik fabryki Matt Carter zdecydował się na zwykły beż. Jobs nie ustępował jednak swojemu charakterystycznemu uporowi, dopóki jedna z najdroższych maszyn, pomalowana na jasnoniebieski kolor, przestała działać tak, jak powinna, z powodu farby. W końcu Carter odszedł – spory z Jobsem, które również często toczyły się wokół absolutnych drobnostek, były, według jego własnych słów, bardzo wyczerpujące. Cartera zastąpiła Debi Coleman, dyrektor finansowa, która między innymi zdobyła doroczną nagrodę dla pracownika, który najbardziej wspierał Jobsa.
Ale nawet ona nie uniknęła sporu o kolory w fabryce. Tym razem było tak, że Steve Jobs poprosił o pomalowanie ścian fabryki na biało. Debi argumentowała zanieczyszczenie, które nastąpi już wkrótce w związku z funkcjonowaniem fabryki. Podobnie nalegał na absolutną czystość w fabryce – aby „można było jeść z podłogi”.
Minimalny czynnik ludzki
Bardzo niewiele procesów w fabryce wymagało pracy rąk ludzkich. Maszyny były w stanie niezawodnie obsłużyć ponad 90% procesu produkcyjnego, w którym pracownicy interweniowali głównie wtedy, gdy konieczna była naprawa usterki lub wymiana wadliwych części. Zadania takie jak polerowanie logo Apple na obudowach komputerów również wymagały interwencji człowieka.
Operacja obejmowała także proces testowy, zwany „cyklem wypalania”. Polegało to na wyłączaniu i ponownym włączaniu każdej z maszyn co godzinę przez ponad dwadzieścia cztery godziny. Celem tego procesu było upewnienie się, że każdy z procesorów działa tak, jak powinien. „Inne firmy po prostu włączały komputer i tak go zostawiały” – wspomina Sam Khoo, który pracował na miejscu jako kierownik produkcji, dodając, że wspomniany proces pozwalał niezawodnie i przede wszystkim na czas wykryć wszelkie wadliwe komponenty.
Fabrykę Macintosha przez wielu określano jako fabrykę przyszłości, demonstrującą automatyzację w najczystszym tego słowa znaczeniu.
Książka Leandera Kahneya „Tim Cook: The Genius, który zabrał Apple na wyższy poziom” ukaże się 16 kwietnia.
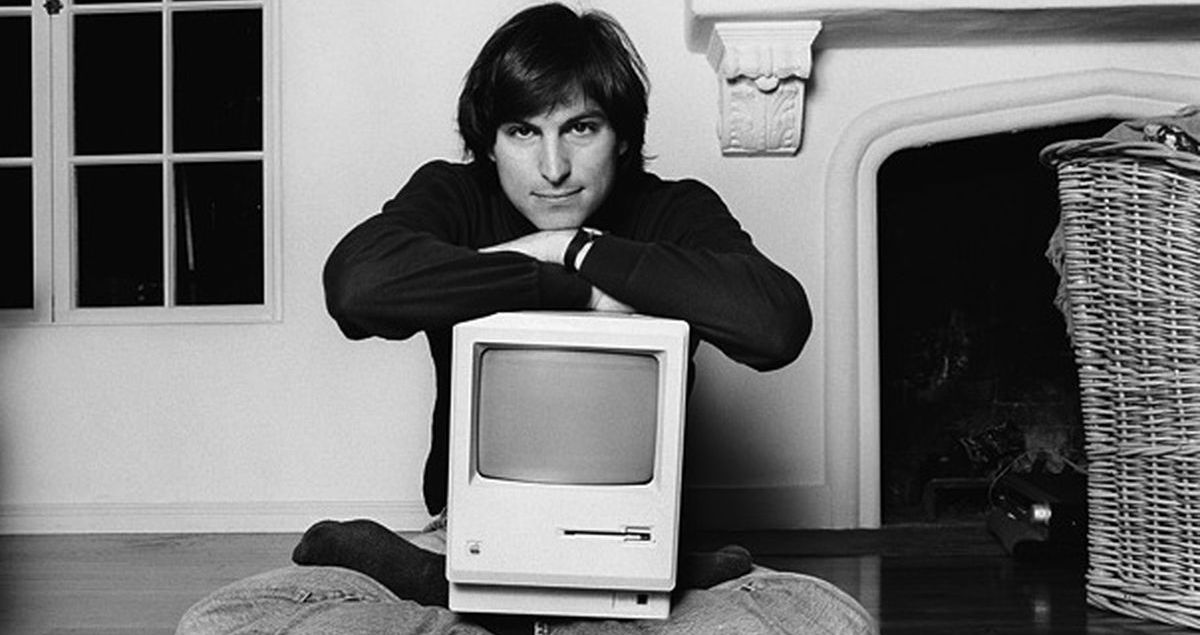
Fabryka o powierzchni ponad 120 stóp kwadratowych… Hmmm, wiem, że jest to magiczne „więcej niż”, więc mogłoby to być około 120 tys. metrów kwadratowych, ale jednak. Musiała to być nie tylko wysoce zautomatyzowana, ale także wysoce zminiaturyzowana fabryka. :-)